The HTM Legacy
Quality machining is in our blood
HTM has been a family owned and operated machine shop for 25 years. Owners Gary and Melinda Bodukoglu, joined Melinda’s parents, Rick and Linda Jones, shortly after the company was founded in 1995. Together they worked to establish and grow a thriving machine shop. In 2011, Gary and Melinda assumed sole ownership and, have continued to invest in innovation and industry education and training to enable the highest quality work and customer satisfaction. Their unwavering dedication and passion for HTM is what makes it a World Class Machine shop today.
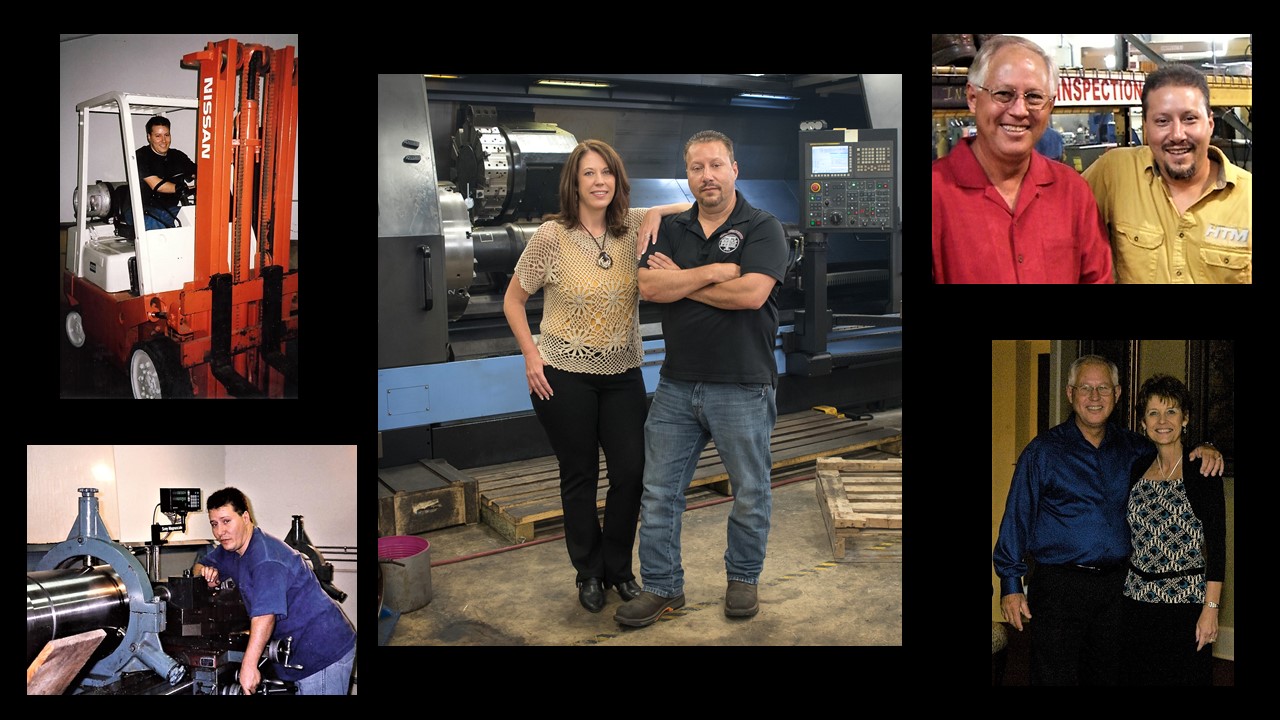
Our Facility is Equipped to Handle Your Needs
HTM operations are headquartered in a 20,000+ square foot building in Houston Texas. Situated on several acres of land, HTM is poised and ready for future growth and the expansion necessary to effectively serve our customers.
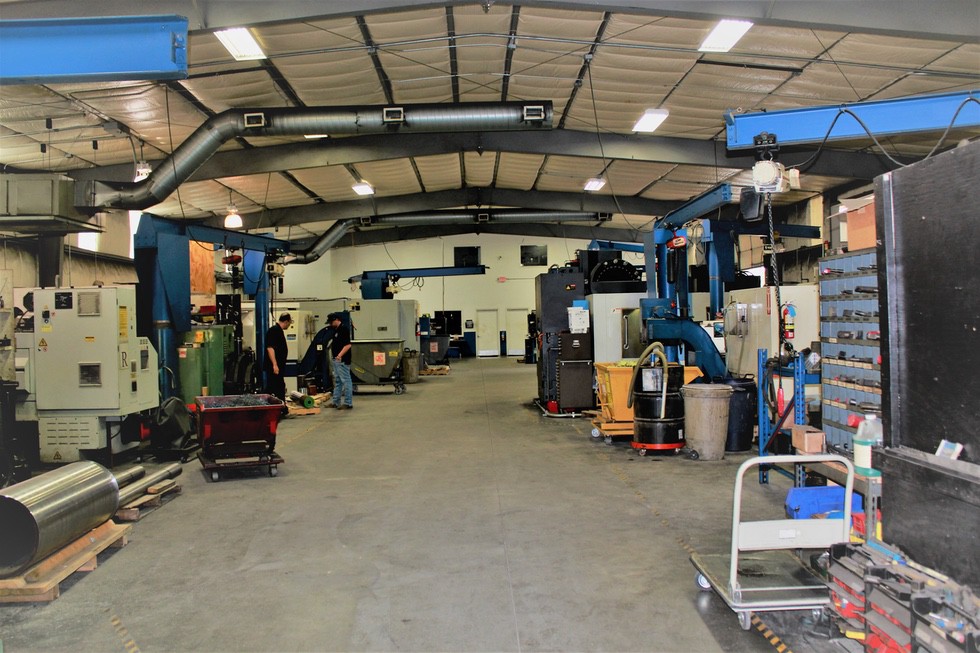
The HTM Workforce is second to none
The HTM Team is highly talented and dedicated. We not only recruit experienced machinists, we believe in investing in our current employees by providing opportunities to work their way through the ranks. Many of our employees have started as shop helper, delivery driver or deburr and worked their way up to 1st Class Machinists, Lead Man and CNC programmers. Investing in our employees by providing ongoing job and safety training helps create an optimistic environment that ensures we retain highly skilled, dedicated workers that set us apart from other machine shops. More than 40% of our employees have been with us 10+ years. Our HTM team is united in the Company Mission and Quality Policy to produce outstanding products for valued customers.
Customer collaboration and satisfaction are paramount
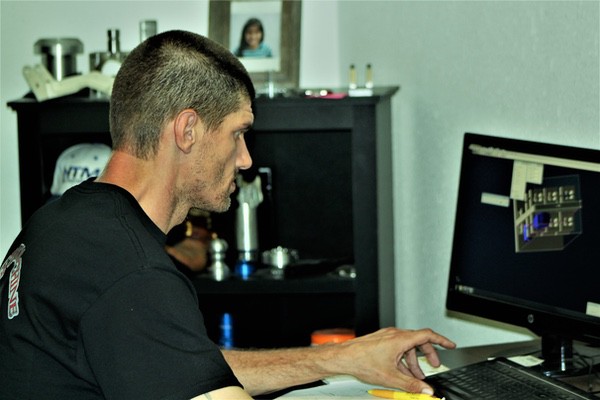

It is this clear process and a high level of teamwork and collaboration that enables HTM to minimize risk, improve performance, and reduce costs while also ensuring a safe and productive working environment.
We provide exceptional service. Over the last 25 years, we have refined a highly effective, collaborative process that ensures the parts we produce function exactly as planned and fully meet our customer’s expectations.